AM Post Process &
Dyeing – Steam DYEING
The IntegrAM Team is aimed at continuous technological updating with primary attention to the needs of our customers, combined with a multidisciplinary vision and attention to environmental sustainability and circular economy. The Steam DYEING project provides solutions for vibratory bowl systems, designed for mass Steam Dyeing of medium/small parts, whether they are in plastic, composites (in particular with a polymers+fiber base) or other compatible plastic materials. A new range of pigments for dyeing has been improved and optimazed by DCL (Dyeing Colour Lab), in a Joint R&D program with the IntegrAM Team, special colouring pigments for any dyeing process – but with priority to the program: EXTRA-BLACK-AM.
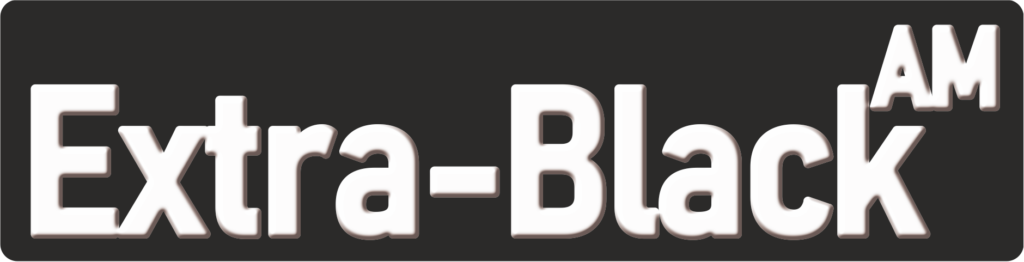
Such an intense and deep black pigment, applied with the Steam Dyeing technology, provides innovation, low waste emission and circular economy concepts. In fact:
The result of this international cooperation is a very modern technology based on three strong points:
- The lowest possible carbon footprint and production of polluting substances or waste – compared with the classic technology about 10 to 20 times less polluting – this means a RATIONAL WASTE MANAGEMENT, with consequent reduced costs;
- Integrated process, 100% automated, including:
2A. Surface preparation; Heating up of the workpieces batch;
2B. Heating up of the workpieces batch;
2C. Steam DYEING EXTRA-BLACK-AM (with reduced quantity of consumables then low waste produced);
2D. Final Rinsing;
2E. Hot Air Drying of the workpieces batch; - Repeatability towards recipes, with final automatic colour recovery, separated by the other phases (i.e.: rinsing)*;
* | In course of development the program to recover exhaust dyeing pigment as a second raw material to produce coloured products;
EXTRA-BLACK-AM technology is going to be revealed at FORMNEXT 2024 in Frankfurt – Germany.
Besides the dark colour trend, we are going to present, in the beginning of 2025, the excellence of colour dyeing with:

GSC Technology – Green Super Coat
Green Super Coat is a metal surface coating technology thanks to which it is possible to coat small metal components with a variable thickness from 120 to 200 microns of Rilsan® – a type of polymer (Polyamide family) with characteristics similar to PA11 or Polyamide 11.

Produced from castor oil, Rilsan® PA11 resin is a high-performance polymer of 100% renewable origin. Rilsan® PA11 resin has been a reliable source of performance in highly demanding applications for 70 years. Since its inception, it has been synonymous with performance and durability.
Source: Click here
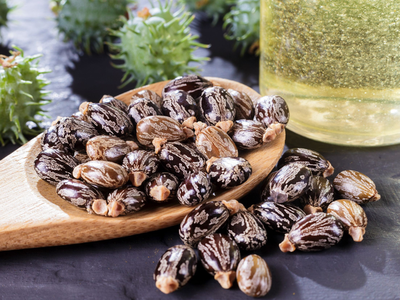
Rilsan® PA11 is easy to process using most processing technologies (extrusion, extrusion blow molding, injection molding, rotational molding and 3D printing).
An “alternative” technology compared to those mentioned above is represented by the application to surfaces with CSC technology where:
- Rilsan® PA11 is used in powder form, brought to certain temperatures using special systems
- The components to be coated are heated, then immersed in this powder
- In a final and further step, the components thus coated are finally heated in a “distension” system where the coating obtained (initially porous) becomes smooth and shiny
The most used and most competitive color of Rilsan® PA11 powder today is WHITE, but it is also possible to coat components with natively black or gray powder. However, starting from the White color, it is possible with a special Steam Dyeing process (or “Steam Dyeing” Techno Surface Patent) to obtain different colors, such as blue, green, red, yellow, light blue, etc.
Some examples in the photo gallery:
I-AM Post Process & Finishing – RotoPAINT
The synergy between the companies of the IntegrAM Team is aimed at continuous technological updating with priority attention to the needs of our customers, combined with a multidisciplinary vision and attention to environmental sustainability and circular economy. The RotoPAINT project provides solutions for rotary-barrel mass painting of small parts, whether they are in metal, plastic, composites (in particular with a wood base) or other compatible materials.
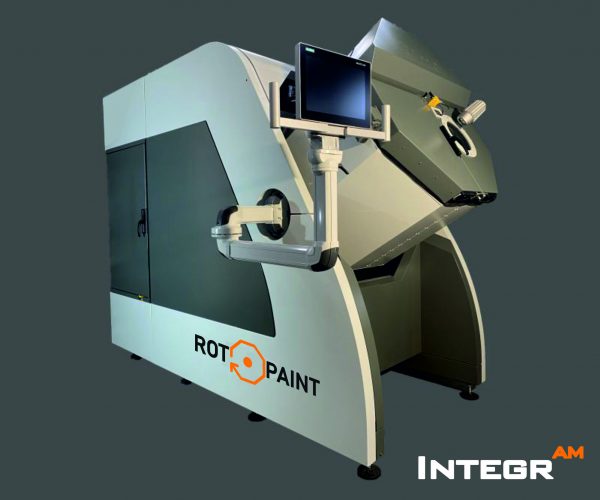
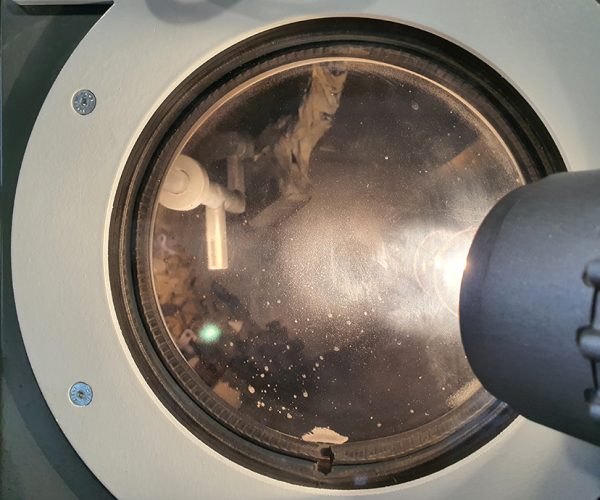
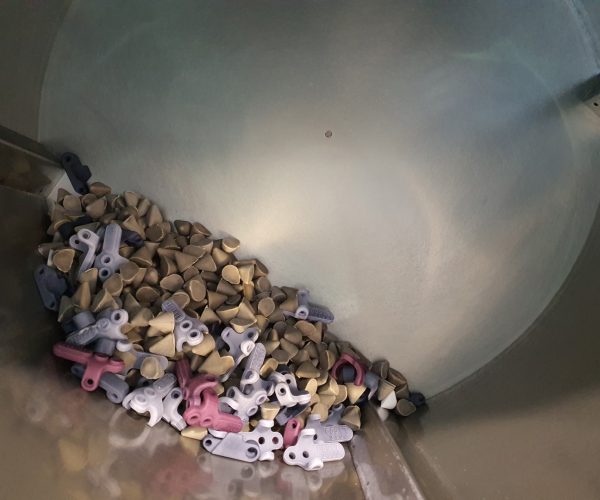
RotoPAINT i4-220 is a system that has reached the maximum expression of technological maturity, compatible with Industry 4.0 standards and with ATEX safety levels, it allows the use of solvent-based or water-based paints.
IntegrAM is constantly looking for solutions that make cutting-edge technologies interact in certain sectors, such as advanced industry 4.0 rotary-painting systems, with QF (Patent pending – I) elastic media. Plants such as RotoPAINT i4-220 are also available for use in Additive manufacturing with this technological innovation, capable of ensuring homogeneous results free from marks or streaks, when the geometries are particularly “difficult”.
Catalogue RotoPAINT
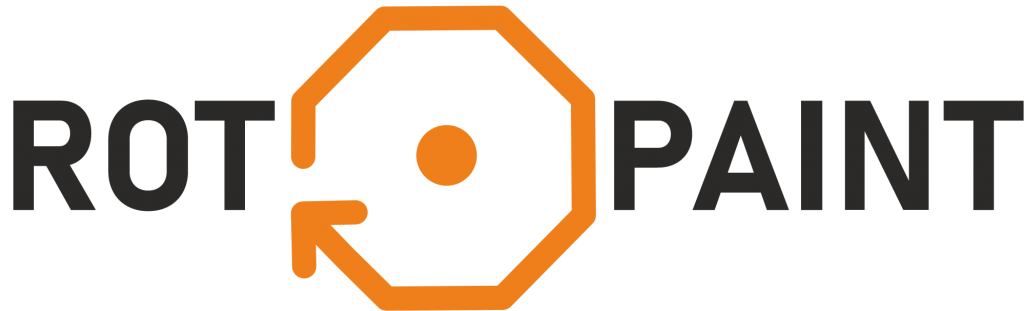
The RotoPAINT logo was created specifically to emphasize how, for the Additive Manufacturing sector, there is an extra gear, offered by the QF roto-varnishing media solution, resilient and formulated to be able to deal with delicate processes on critical items.